數字技術能為傳統高耗能行業帶來怎樣的改變?一張基于工業互聯網平臺開出的數字化“藥方”,正助力廣西、山東、新疆等地重點企業實現電解鋁工藝管控的標準化智能化,可為企業帶來數千萬元年化節降效益。
近日召開的“2023·廣域銘島電解鋁高質量發展論壇”上,廣域銘島解決方案專家分享了數字化節能降碳“術”,引發行業頂級專家學者及業界代表們的深入探討。

以數字化方式實現電解槽工藝自優化
鋁是金屬里面僅次于鋼鐵的重要戰略資源,是發展航空航天、新能源汽車、動力電池、電子信息制造等新興產業的重要支撐。
相關數據顯示,當前我國電解鋁行業噸鋁綜合電耗在13300多千瓦時,運行產能穩定在4000多萬噸,是工業領域絕對的耗電大戶,也是國家“雙碳”目標下節能治理的重要環節。
在節能降碳上,行業中有不同的探索路徑,包括低碳冶煉技術、清潔能源電解、節能槽設計等,其中電解槽工藝數字化管控是有效且必要的手段。
“電解槽電解過程用電占噸鋁電耗的90%,但傳統企業在電解槽工藝管控上,難以擺脫依賴個人經驗的泥潭,使得工藝標準不統一、執行不到位,易出現槽況不穩而導致電耗增加。通過數字化管控可以有效解決這些問題。”
廣西百礦集團工藝研究專家易勇廳介紹,百礦集團與廣域銘島共同探索數字化節能降碳,基于Geega(際嘉)工業互聯網平臺,搭建了電解鋁智能分析平臺,集成電解槽槽控數據、質量化驗數據、溫度等測量數據等多環節數據,以槽狀態、工藝參數和槽分類三大標準對電解槽做綜合判斷,并給出操作建議,有效解決了“有監控沒結論、人工判斷隨意性大”等問題。
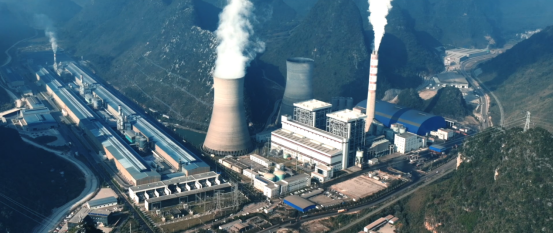
▲百礦集團德保基地
不僅如此,通過數字化方式還可以實現電解槽工藝的自優化。廣域銘島節能降碳解決方案專家黃勇彪介紹,數字化的工藝管控除了要標準化,更要智能化。“在工藝知識、經驗數字化封裝的基礎上,運用機器學習和統計學的理論和方法,可以持續挖掘潛在優化空間,并通過數字化閉環管控進行固化、沉淀,完成滾動尋優。”
在百礦德保基地,上述數字化智能化的工藝管控,落地實施不到一年即獲得超2500萬節降效益,實現“一個平臺,兩大改變,三大提升”——即建立一個具有電解鋁行業特色的大數據智能分析平臺,改變工藝決策思路和知識傳遞沉淀,提升管理水平、決策效率和經濟效益。
通過爐膛仿真輔助工藝提升
“工藝管控的標準化和智能化,本質是基于現有的數據沉淀和專家經驗,以數字化方式來做固化和提升。但我們還可以做‘增項’,實現更深度數字賦能。”廣域銘島基于Geega(際嘉)平臺的數據采集和解析能力,開發電解槽爐膛仿真系統,通過槽況監測和分析指導電解槽工藝管控。
爐膛是電解槽啟動初期在內部四周生成的一層固體結殼。規整的爐膛可起到保溫作用,降低電解槽熱損,減少能量輸出,同時也能保護電解槽側部不被熔融電解質腐蝕,增加槽壽命。因此,對爐膛進行動態監控,能給工藝管控和電解槽管理提供有效決策指導。
“實現爐膛的動態在線監測很難,因為電解槽內部900多度高溫和強磁場,有很多無法直接用數學模型表達和量化的非物理量,比如內部的熱對流、熱輻射方式和比例等。”廣域銘島電解鋁專家赫耕介紹,由廣域銘島自主打造爐膛仿真系統,基于三鋼溫度、電解槽實時運行數據、工藝參數,運用算法、大數據、機器學習,可以得到電解槽內部爐膛變化趨勢,實現高時效性的爐膛仿真,為電解槽的長期高效穩定運行提供數據支撐,保證產量與質量、減少熱損失、節約電耗、延長槽齡。
目前,爐膛仿真系統應用在部分電解鋁廠,已取得了良好成效,正在更多生產基地進行應用和推廣。
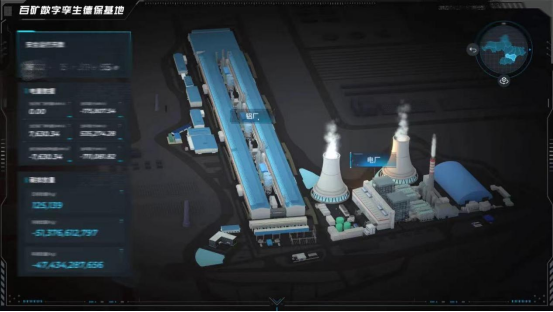
▲百礦集團德保基地數字孿生工廠
同時,孿生輔助決策的方式,也從設備層擴大到產線、車間、整廠及集團。在百礦集團,廣域銘島助力企業構建了數字孿生鋁廠和電廠,實現了數字世界對物理世界的實時還原和反向指導。“在電解鋁、鋼鐵、焦化、磷化工等高耗能行業,孿生、運籌優化、AI算法、機器學習等數字技術還將有廣闊的應用空間。”
從能源密集型向環保型轉變,從低效生產到高效生產,電解鋁行業正經歷著蛻變。廣域銘島將攜手更多的“創變者”和“攀登者”,持續為行業數字化發展貢獻更高價值的解決方案,同時基于高耗能行業共性特點,加速數字技術賦能,推動高耗能行業實現綠色低碳的進化。